More importantly, the schedulers and planners do not have a tool that enables scenario planning, which is a leading practice for evaluating trade-offs and outcomes, while maintaining operating policies and scheduling rules. In addition to cookies that are strictly necessary to operate this website, we use the following types of cookies to improve your experience and our services: Functional cookies to enhance your experience (e.g. These components include the physics-based formulations; the statistical analysis of data from the sensor network; the real-time data; the pre-performed localized in-depth simulations to predict activities of the corresponding physical twin; and the system Genome with a digital thread that connects all these components together. Integrating in real time with systems across the plant and enterprise, digital twins act as a cerebral cortex of the plant, synchronizing processes, labor and flow, thereby maximizing your return on industry 4.0 investments. Patwal: In power generation, digital twin refers to the mapping of the physical asset models in a digital platform, where a virtual digital replica model is created. The digital twin will schedule around downtime of machines, which gives schedulers and planners a key tool in agile production scheduling. In high-speed manufacturing environments, clients with digital twins are rescheduling multiple times per day. The available research on DT for power plants is limited and lacks details on DT comprehensiveness and robustness. For more information about our organization, please visit ey.com. EY refers to the global organization, and may refer to one or more, of the member firms of Ernst & Young Global Limited, each of which is a separate legal entity.
The modeling in is created using information from massive amounts of design, manufacturing, inspection, repair, sensor, and operational data and is constantly updated with asset data. This concept has been further extended to industrial scenarios and is often referred to as Industrial Internet of Things (IIoT). Using a plant digital twin, you can model the system dynamics and manufacturing complexity needed to answer significant questions that will determine the future. The Power Plant of the Future 4.0 goals are pushing the territories of power plant operations and maintenance toward an autonomous scenario to reduce costs and increase revenue. By continuing you agree to the use of cookies. Future Consumer Index: In crisis, but in control. Classic Association for Operations Management methodology utilizes levels of capacity planning within the organization that range from long-term (resource planning) to short-term (finite). How Utilities Can Manage Supplier Risk [PODCAST], digital twin is the usage of the right software to analyze and visualize data, digital twin performs asset life estimates, detects behavior anomalies, and calculates thermal efficiency, Digital technologies are transforming the power generation industry, satisfy their specific requirements around operational flexibility, maintenance optimization, and enhanced planning, Utilities need to realize that they must embrace digitalization, Digital Twins and Remote Monitoring Address Changes in the Energy IndustryQuickly, New Monitoring and Analytics Tools Improve Plant Performance, The POWER Interview: How Gas Power Can Reap Value from Digitalization, Siemens strengthening digital T&D portfolio with new substation tech, transformer diagnostics, power grid digital twin, It's Not About Base Load Performance Anymore, From the Lab to the Field: Making the Most of Your Microgrid, "The use of advanced simulation in the design of the Xe-100 Advanced Reactor Power Plant". The digital twin enables smarter management of the sectors energy resources.
Ensuring that these moves will accomplish the expected returns can be achieved through solutions like digital twins to pressure-test potential choices. Enabled by data and technology, our services and solutions provide trust through assurance and help clients transform, grow and operate. Across many facets of your operations, these virtual environments make hidden opportunities visible to drive real-world results, acting as laboratories to reimagine what you do and how you do it with speed, agility, and resilience. For each level, there are different techniques (i.e., capacity planning using overall factors, capacity bills or resource profiles) used to establish the capacity factors, which drive the estimated capacity that do not account for current inventory levels, use factors that are aggregated average of averages, and overall yield different results from the short-term finite schedules. Sales Policy Copyright 2022 Elsevier B.V. or its licensors or contributors.
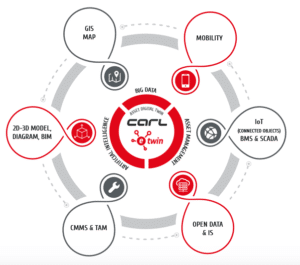
Probability distributions are available for modeling demand fluctuations, allowing the model to predict failure points and potential bottlenecks. Power producers today need to address multiple changes to the energy industry that are coming fast and furious., Industrial Internet of Things (IIoT) technologies can help make electric generating plants more efficient while increasing availability. Digital twins can be used to replicate the physical and operational characteristics of a power generation plant or other utility asset prior to construction and also to help improve operations and maintenance over the useful life of physical installation. The digital twin becomes the cerebral cortex of the shop floor, planning and orchestrating all interconnected processes. Data-driven approach alone is not sufficient and a low order DSM is needed. Published by Elsevier Ltd. https://doi.org/10.1016/j.egyr.2022.02.305. Companies can leverage on plant digital twins to measure capacity, perform activity-based costing and rapidly model operations. Leading plant digital twin solutions can run experiments with statistically significant replications to provide the company with a high level of confidence in the results. Disparate IT systems and outdated planning technology hampers speed in decision making. A multidisciplinary team is developing digital twins of nuclear reactors with the help of a $5.2-million grant from the Department of Energys Advanced Research Projects AgencyEnergy. The main focus of the present study is to propose a comprehensive and robust DT architecture for power plants that can also be used for other similar complex capital-intensive large engineering systems. But with the advent of newer data sources and data management approachescomplimented by analytical capabilitiesnewer opportunities are being envisioned for greater understanding of customers business needs and power plant equipment dynamics.
POWER: How is technology changing power plant operation today? The digital twin performs asset life estimates, detects behavior anomalies, and calculates thermal efficiency to ensure that the operations and maintenance processes are optimized across the power plant. Because plant digital twins are connected to real-time data, reflect the stochastic nature of the actual shop floor, and model complex system dynamics, they offer tremendous value in plant production scheduling. We know the breakdown will occur, but we just dont know when or for how long. The team is made of faculty at the University of Michigan, senior scientists at Idaho National Laboratory and Argonne National Laboratory, and industry partners at Kairos Power and Curtiss-Wright. Review ourcookie policyfor more information. In our experience, the aggregated, longer-term capacity analyses overstate capacity by 10 to 20% due to simplifying planning assumptions. Some of the key goals of the digital twin are cost savings, revenue increase, reduced outages, improved operations, and market dynamics management. He has been pioneering the building of digitalization and big data-based framework by developing and implementing company-wide platforms, systems, and business processes to maximize the value of enterprise data, driving performance improvement, cost reduction, and revenue generation. COVID-19: How to protect your supply chain. New algorithms needed to predict systems dynamic behavior with data-driven methods. Calle lvaro de Bazn, 10 Pasaje de la luz
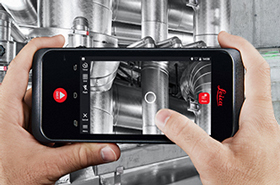
The insights and quality services we deliver help build trust and confidence in the capital markets and in economies the world over. A plant digital twin incorporates the probability of failures across all machines in the process, while traditional planning systems choose to ignore the Murphys Law of inevitability. EY helps clients create long-term value for all stakeholders. To be competitive in uncertain markets and save money, companies need to look at varied scenarios by analyzing real-time data streams generated by power plant operations, planning, and maintenance. Weve got you covered! 46010 (Valencia, Spain), Subscribe to our newsletter and stay updated. Unfortunately, weve worked with many clients that did not have this capability and were significantly impacted financially as a result. [], Nowadays, we can find more and more optimized, digitized and efficient infrastructures. The term digital twin is used frequently by tech-savvy power industry professionals, but what does it really mean? The acid test for a plant digital twin is its capability to capture the dynamically changing constraints on the shop floor, so that management can now sense the necessary rate of change for the business model and respond with a feasible plan. In the industry, digital twins refer to the mapping of physical asset models on a digital platform, where a virtual replica of any physical object or process is created. How will my manufacturing footprint need to change given how we expect the product portfolio and customer base to evolve for 2030, and how will that impact our capital allocation planning? Digital twin can simulate scenario plan needed to make data-driven decisions. In this framework, an environment of real objects (equipped with sensors and software) and other technologies is created with the aim of exchanging data through the Internet, which can then be processed by this technology. For greenfield operations or significant capital investments to existing manufacturing footprints, digital twins can be deployed to evaluate the design before allocating capital. Its capability to diagnose problems within complex systems differentiates digital twin from traditional scheduling system. This virtual model is built using information from massive amounts of design, manufacturing, inspection, repair, sensor, and operational data. Develops tools to boost performance. It intends to provide the following capabilities in power generation: Aaron Larson is POWERs executive editor (@AaronL_Power, @POWERmagazine). This is created using the asset-related data obtained from various sources, combined with deep domain knowledge about the asset. How digital twins give automotive companies a real-world advantage. Discrepancy between DSM and ADL requires in-depth localized off-line simulation LDS. It has led to the introduction of Internet of Things (IoT) in the power generation industry. All Rights Reserved. A digital twin provides a testing ground for monitoring, simulating, and optimizing production, quality, and operational performance. In our experience, we have seen tremendous benefits using a plant digital twin across sectors, including manufacturing. 2022 The American Society of Mechanical Engineers. 64% of manufacturers say reshoring is likely following pandemic. Patwal leads the development and commercialization of digital business transformation projects, using big data platforms and analytics, to create data-driven services. This allows the operator to understand operations of the asset and prevent unexpected failures. Traditional modeling approaches involved running deterministic spreadsheet simulations or solvers whenever the business was confronted with a key decision. Some of the key goals of the digital twin are cost savings, increased revenue, reduced outages, improved operations, and managing market dynamics. When using a plant digital twin, users can assess constraints across materials, resources, labor, and time to diagnose the current bottleneck. Problem solver. You may withdraw your consent to cookies at any time once you have entered the website through a link in the privacy policy, which you can find at the bottom of each page on the website. They give you insights into questions such as: Plant digital twins can model these scenarios to help management evaluate trade-offs and consider second-order effects (each consequence has another consequence) that planning systems and spreadsheets are simply incapable of considering quickly. Then, the requirements and rules for the power plant DT are established and the major DT components are determined. 2022 The Author(s). The digital twin provides the critical lenses needed for executives to make decisions: the operational key performance indicators and the impact to the financials. The other key aspect to a digital twin is the usage of the right software to analyze and visualize data, which allows operators to manipulate digital asset conditions for scenario planning without interfering with the operation of the physical asset. ScienceDirect is a registered trademark of Elsevier B.V. ScienceDirect is a registered trademark of Elsevier B.V. Digital twin in energy industry: Proposed robust digital twin for power plant and other complex capital-intensive large engineering systems, Anomaly Detection and deep Learning (ADL). Skilled at leading enterprise and plant-level improvement transformations. The, Digitalization is furnishing nearly every facet of the power industry with new insights that promise value for generating, DENVER -- At this years IEEE T&D Conference (Booth #1242), Siemens announced a strengthened digital T&D portfolio across. Auto regression to predict anomalies performs better when system is not dynamic.
With digital twins, it is possible to massively manage very complex industrial processes that require a strict integration architecture and industrial automation to be efficient. Leonard, M. (14 May 2020). Embedding the advanced scheduling algorithms into a plant digital twin can generate feasible schedules at scale and speed, boosting throughput 5 to 10% while significantly reducing cost. 2022 The American Society of Mechanical Engineers. The current plant digital twin technology can simulate a wide range of reliability and yield curves. The digital twins connectivity is bidirectional, which allows it to send task lists to the shop floor as part of the overall schedule. Digital twins can increase efficiency of these new investments by 20% to 30% through simulating the new factory in the virtual environment. A plant digital twin production scheduling application is connected to the shop floor manufacturing execution system (MES), enterprise resource planning (ERP) system, and planning systems, which allow it to sense and respond to machine downtime events, poor yields, and changes in product mix. Contact us for advice on how to achieve a global operating environment with digital twinning technology. Proactively bringing these scenarios to management is a competitive advantage. IoT is the network of interconnected devices or things embedded with sensors, network connectivity, data management systems, and analytics engines to collect, manage, and analyze data to generate actionable resources. It also allows cross collaboration with other industries, which have similar dynamics as the power generation industry. Traditionally, most of the data generated within the power industry was limited to remote monitoring and diagnostic services, where it was analyzed to monitor turbine operations. A plant digital twin models the structural complexity of processes, multilevel bills-of-material, key constraints, product shelf life, labor skill levels, and complicated decision rules, but just as importantly, it captures and simulates the stochastic nature of the shop floor. How are we going to answer our customers requests for more variety and shorter lead times? The complex future power plants require digital twin (DT) architecture to achieve high reliability, availability and maintainability at lower cost. The latest digital twin solutions create a production schedule incorporating decision rules, evaluation criteria, and key performance indicators, which are coupled with the latest system data to generate a set of prescriptive actions for planners to ensure the right decision is made. Every day, more and more companies are joining the Fourth Industrial Revolution or Industry 4.0. Plant digital twins are valuable in production scheduling due to their real-time data and ability to reflect the stochastic nature of the shop floor. How can I ensure that my capital allocation decisions will generate the highest returns for the company? In addition, it allows understanding and modelling the performance of, for example, a power plant by representing its state, operation or position, almost in real time. In fact, reports such as KPMGs Beyond the hype of i4.0 clearly identify this technology as a key tool to achieve Industry 4.0. Please refer to your advisors for specific advice. Because plant digital twins can measure capacity across time periods, perform activity-based costing and rapidly model operations, companies can leverage them to improve their decision-making process for allocating capital. This material has been prepared for general informational purposes only and is not intended to be relied upon as accounting, tax, or other professional advice. Sitemap IIoT plays a key role in the integration of OT and IT networks, and lays out a comprehensive sensor network to generate operational and system data, provides a data management module to manage data, and an analytical backbone to analyze data to discover new insights, provide prescriptive recommendations, and take necessary actions. In so doing, we play a critical role in building a better working world for our people, for our clients and for our communities. But one of the limitations of this technology is that it can be difficult to implement, due to a lack of open source software and interoperability issues. With this technology, electrical operators manipulate the conditions of digital assets for scenario planning without interfering with the operation of the physical asset. Plant digital twins run scenarios based on mix, alternate routings, crew schedules, projected interruptions in supply, and interruptions due to machine downtime. The digital approach goes beyond simply gathering data or offering a software program, by integrating structured and unstructured data from different sources, and performing insight-driven analytics on it to provide recommendations to improve plant performance and optimize maintenance. 2020 EYGM Limited. That is why digital twins are a key piece in industries such as electricity, since they allow controlling all energy resources distributed in the network and have the appropriate software to analyse and visualise all data. What are the challenges associated with plant digital twin? All rights reserved. We recently worked with a leading OEM supplier, and our process digital twin was able to increase throughput of a new line by 40%, saving $750,000 per month through debottlenecking the design virtually. The result is more accurate single source of truth on capacity and a lot less conflict between corporate and the plants. Defense Daily subscriber and registered users, please log in here to access the content. For example, the plant digital twins algorithm will determine the best sequence of changeovers for machines, labor schedule/shift requirements, and material arrival times at corresponding operations. Asking the better questions that unlock new answers to the working world's most complex issues. The ingestion and structuring of real-time and historical data offered by the Nexus Integra platform allows the implantation of reliable Digital Twins that facilitate control, simulation and efficiency in maintenance tasks for plant extensions. Heres what we mean by stochastic nature: Consider a machine breakdown. It is therefore very beneficial for utility companies when planning actions for the future with a large amount of distributed energy resources, such as solar panels, on the grid. All rights reserved. Normally, traditional planning systems generate the schedule on a weekly basis, which causes a natural and recurring dissonance between the schedule and the current state of operations. The ability to schedule the facility requires connectivity to the MES and ERP systems. Lastly, a fundamental issue with these traditional capacity planning tools is rooted in the deterministic nature of the underlying model, which assumes no randomness. How do you move long-term value creation from ambition to action? Since the digital twin is a virtual replica of a system, solutions to current bottlenecks can be tested in a risk-free environment. Proposed new, robust and comprehensive Digital Twin architecture for power plant. This technology makes it possible to establish an optimal strategy for daily or hourly operation based on the weather forecast or the price of electricity, and to predict maintenance operations when the efficiency level falls below a certain value. The digital twin is a new form of intelligent management that makes networks infinitely more data-oriented, forward-looking and with a global vision of the environment that surrounds them, which makes them more sophisticated and dynamic. This enables companies to centralize important aspects of system and process management, and outsource desired services. 2022 The American Society of Mechanical Engineers. Here, we take a look at the eight key benefits to a plant digital twin. While both IIoT and IoT have the same main character, that is, availability of intelligent and connected devices, in most cases, IoT is used in the consumer domain and IIoT is prevalent in the industrial realm. We develop outstanding leaders who team to deliver on our promises to all of our stakeholders. The MES provides the digital twin with the status of equipment and jobs on the shop floor, allowing for automated rescheduling around downtime.